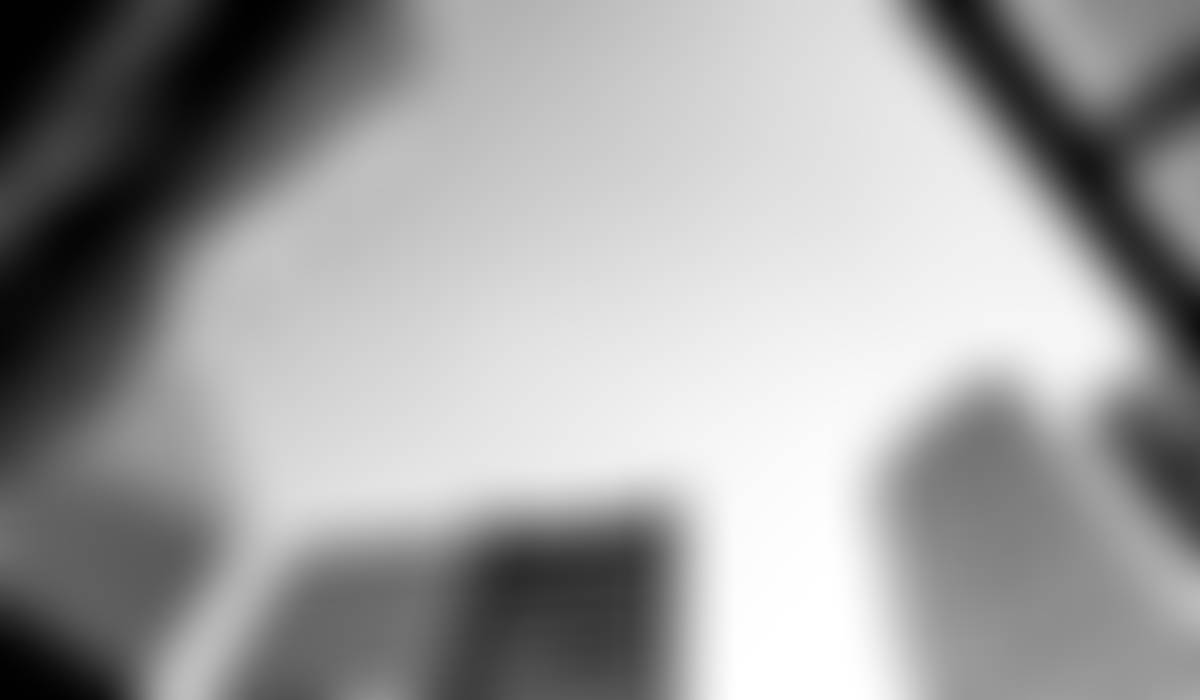
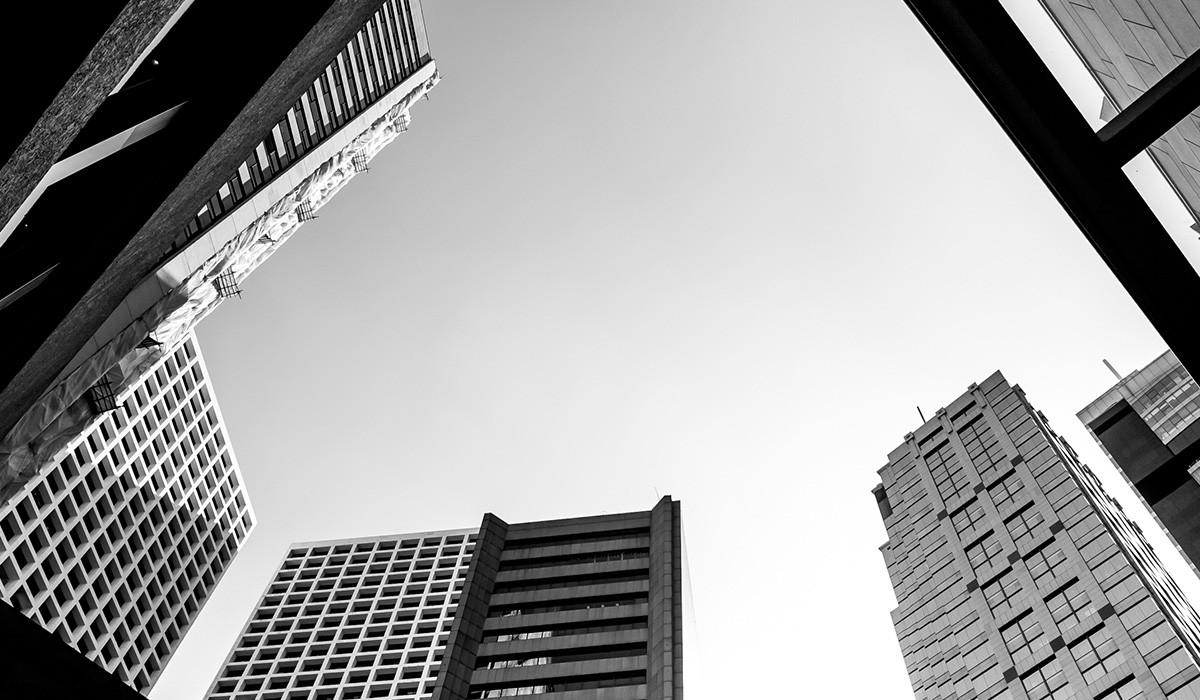
My lovely Average Cost newsletter
July 31st, 2023
In the realm of manufacturing and production, keeping a close eye on costs is of paramount importance for businesses to thrive and remain competitive. Among various financial metrics, the concept of Average Cost stands out as a critical indicator of a company's financial health and operational efficiency. It represents the average amount of money spent to produce a single unit within a production run, offering valuable insights into the cost-effectiveness of the manufacturing process.
The calculation of Average Cost is straightforward - it involves dividing the total cost of production by the number of units manufactured. As the number of units produced during a production run increases, the Average Cost tends to decrease, thanks to the distribution of fixed costs over a larger output.
Understanding and analyzing Average Cost is pivotal for businesses for several reasons. First and foremost, it directly impacts a company's profitability. By keeping the Average Cost low, businesses can increase their profit margins, enabling them to invest in growth, research, and development, or even pass on the cost benefits to consumers in the form of competitive pricing.
Optimizing Average Cost also plays a crucial role in pricing strategies. Companies need to strike a balance between setting a competitive selling price that attracts customers and covers the costs incurred in production. A thorough understanding of Average Cost helps companies avoid pricing their products too low, leading to losses, or too high, risking losing customers to competitors.
Furthermore, Average Cost is an essential tool in cost estimation and budgeting. When planning future production runs, manufacturers can use the Average Cost to estimate the total cost of production and allocate resources accordingly. This aids in preventing overproduction or underproduction, ensuring that demand is met while avoiding unnecessary expenses.
Average Cost also influences decision-making concerning process improvements and investments in technology. By identifying areas with higher Average Costs, businesses can pinpoint inefficiencies and target them for improvement. Investing in automation or streamlining production processes can lead to cost savings and increased productivity, ultimately enhancing the overall competitiveness of the company.
However, managing Average Cost comes with its own set of challenges. External factors like fluctuations in raw material prices or unexpected changes in demand can impact the cost per unit. Additionally, businesses must carefully evaluate the trade-offs between scaling production for lower Average Costs and managing inventory levels to avoid unnecessary holding costs.
In conclusion, Average Cost is a critical metric that holds the key to financial efficiency and competitiveness in manufacturing and production. By understanding and analyzing Average Cost, businesses can make well-informed decisions, set competitive prices, allocate resources effectively, and ensure sustainable growth in a dynamic and ever-changing market landscape. Striking the right balance between cost optimization and meeting consumer demand is the path to long-term success in the industry.
For example if you want to know the average cost of rear main seal replacement.