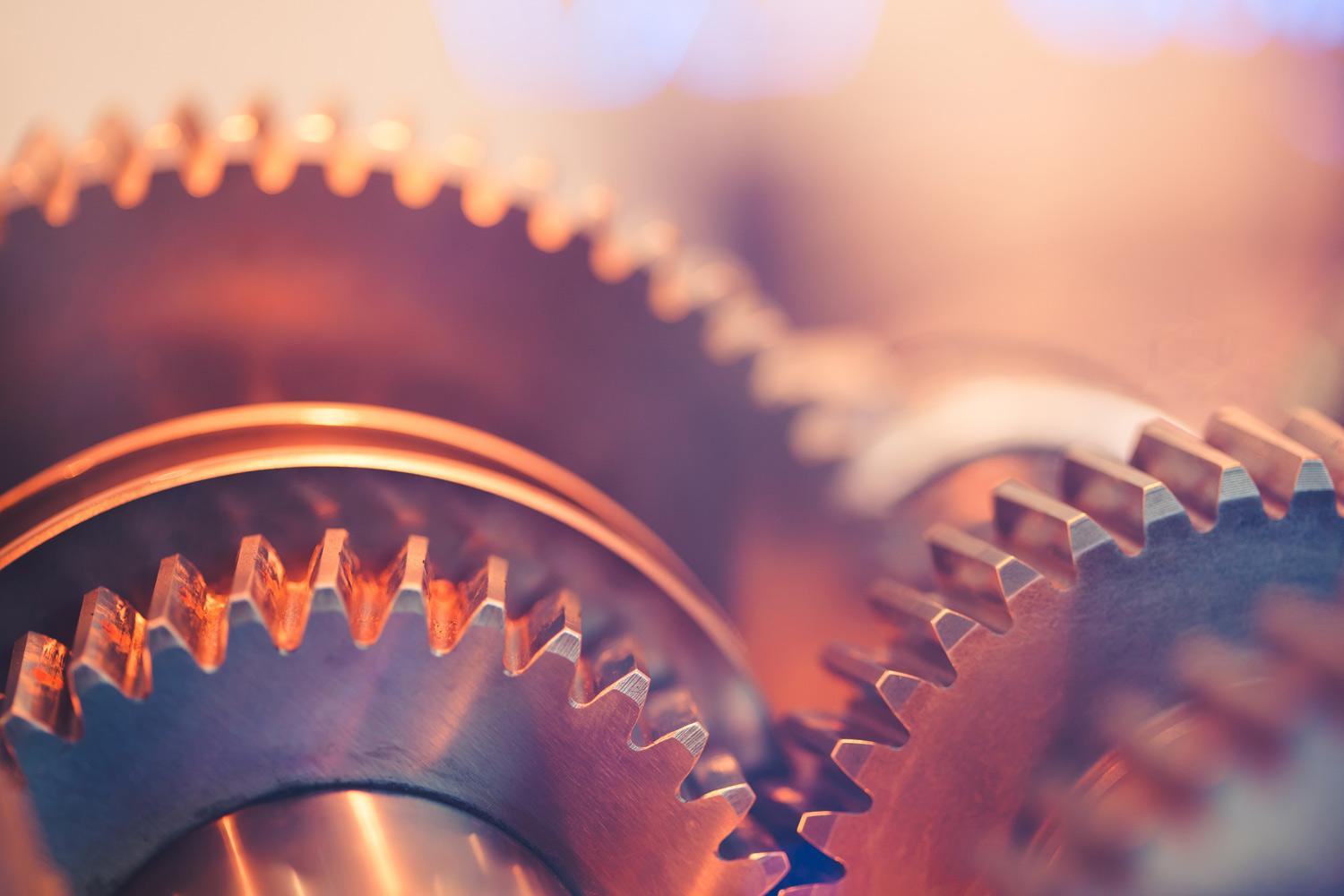
Blow Molding Equipment
Important Features to Look for In Blow Molding Equipment
When it comes to blow molding equipment, it is essential that you work with a manufacturing company that can help you choose the appropriate machine for your specific needs. After all, the blow molding process creates a multitude of products, ranging from water bottles to recyclable plastic furniture.
For example, if your company manufactures plastic bottles for water, soda, sports drinks, household cleaners, milk, and so on, then you need a top-of-the-line bottle blowing machine. You would choose the equipment based on the products that you make and the materials you use. Fortunately, reputable plastic extrusion equipment manufacturers offer excellent assistance as part of the selection and buying process.
For all machines used for blow molding, you need to look for specific features. Following are a few examples of those:
• Heavy duty solid construction
• High impact resistance containers
• High quality screw and barrel composition
• Multi-cavities molding in a single cycle with maximum quality consistency
• Easily controlled wall thickness for the containers
• High precision threads on bottle opening
• Adjustable angled blow pins and extruder platform
• Reduced power consumption for energy saving and product cost reduction
• Self-diagnostic feature with error message displayed on screen
Some additional factors to consider:
• Mold – You need a high-quality mold in the desired shape and size according to the product manufactured. Also, the mold should have several inlets and outlets that work in an oscillating cooling pattern. Otherwise, you could have issues with reproducing surface texture.
• Cooling – The equipment that you choose must have the appropriate cooling mechanism. For controlling the dimension, warpage, and surface appearance of the product, having excellent cooling control is imperative. For the removal of heat and cycle time, the flow rate is an essential factor. The goal is for the machine to create turbulent flow, thereby improving heat extraction and cycle time. For controlling warpage, the mold cooling should offer extra heat extraction in the heaviest wall portions of the part or component. Ultimately, the cooling feature plays a significant role in the overall quality of the finished product.
• Venting – Venting is another critical factor. Once a mold closes the parison, a small quantity of air becomes trapped between the mold cavity and the exterior of the parison. During the blow molding process, air gets blown inside to expand the parison, forcing the trapped air to become compressed. However, because the parison does not fully touch the wall of the mold, it can cause visible defects in the surface, along with creases, draglines, and poor engraving or texture detailing. With venting, slots fit into the edge of an insert inside of the cavity to prevent issues.
When choosing a machine and features, always work with a reputable supplier. Make sure that the company you select understands your blow molding processes, and inquire about the different molding machine sizes based on the weight of the plastic products that you make.
Also, ask whether there is more than one machine that fits your need. Finally, along with the customer service you get while selecting the equipment, go with a company that offers support after the fact. That way, you have a trusted source to turn to if you have a question or run into a problem after having your new machine delivered and installed.
Stellar Machines
For help choosing the right machine based on the products you manufacture, you can always count on our team of experts at PET All Manufacturing. Visit us online or call today for more information.